Understanding Injection Mold Makers: The Pillars of Modern Manufacturing
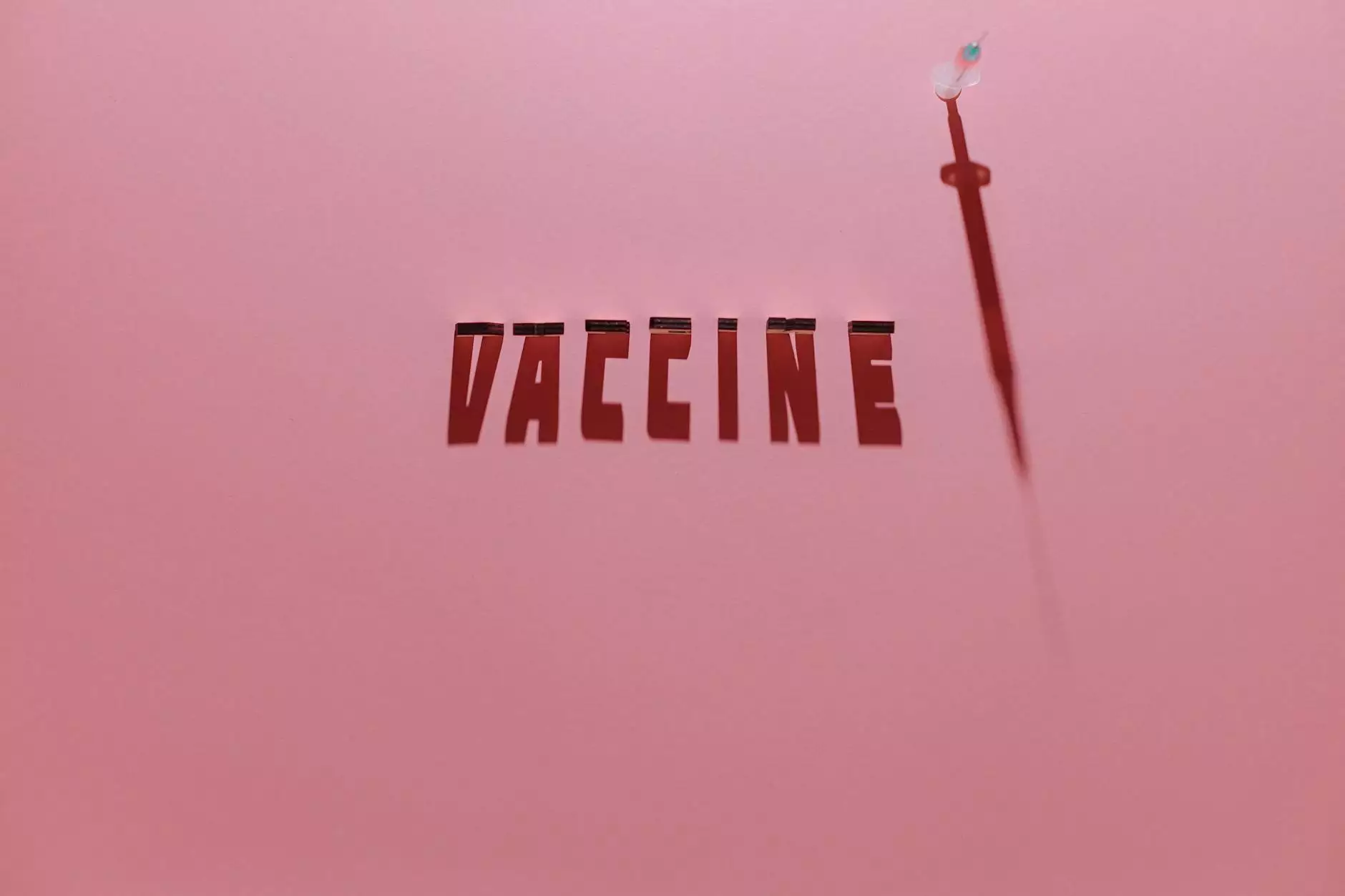
What are Injection Mold Makers?
Injection mold makers are specialized professionals and companies that design and produce molds used in the injection molding process. This process is crucial for creating parts and products across a range of industries, including automotive, consumer goods, medical devices, and electronics. They utilize advanced techniques and technologies to ensure high precision and quality in the parts they manufacture.
The Importance of Injection Mold Makers in Manufacturing
In today's fast-paced manufacturing environment, the role of injection mold makers has never been more critical. They are instrumental in:
- Streamlining Production: Efficient molds lead to faster production rates and lower costs.
- Enhancing Product Quality: Well-designed molds ensure that products meet exact specifications and reduce defects.
- Promoting Innovation: Mold makers work closely with product designers to develop new products and enhance existing designs.
- Reducing Time-to-Market: With rapid prototyping and efficient mold design, businesses can introduce new products more quickly.
The Injection Molding Process Explained
The injection molding process involves several key steps, each of which is crucial for achieving high-quality results:
- Designing the Mold: This is the first and most crucial step, where considerations of part design, material choice, and mold mechanics are established.
- Creating the Mold: Using CNC machining, electrical discharge machining (EDM), and other techniques, mold makers fabricate precise molds from materials such as steel or aluminum.
- Injection: Molten plastic is injected into the mold at high pressure to form parts.
- Cooling: The plastic cools and solidifies in the mold shape.
- Removing the Part: Once cooled, the mold is opened, and the part is ejected.
- Quality Control: Finished parts undergo rigorous testing to ensure they meet specifications.
Materials Used by Injection Mold Makers
The choice of material significantly affects the performance and cost of the molds as well as the final product. Common materials used include:
- Steel: Known for its durability and ability to produce high-quality molds, though it is more costly.
- Aluminum: Lighter and less expensive than steel, excellent for producing prototypes or lower-volume production runs.
- Specialty Alloys: These may be used for specific applications that require unique properties.
- High-Performance Plastics: For molds that involve low-volume specialty products.
Innovations and Trends in Injection Molding
As technology advances, so do the methods employed by injection mold makers. Some current trends include:
- 3D Printing: Increasingly used for creating complex mold designs quickly and economically.
- Smart Manufacturing: Incorporating IoT and AI technologies to monitor production and improve efficiency.
- Eco-friendly Practices: Adoption of sustainable materials and processes to minimize environmental impact.
- Advanced Software: Use of CAD and CAM software for mold design and manufacturing, enhancing precision and reducing lead times.
Choosing the Right Injection Mold Maker
When selecting an injection mold maker, businesses should consider several important factors:
- Experience: Look for companies with a proven track record in the specific type of molding required.
- Technology and Equipment: Ensure they utilize the latest technology and machinery.
- Quality Assurance: Verify their quality control processes and certifications.
- Customer Support: A reliable mold maker should provide excellent support throughout the project lifecycle.
- Cost Structure: Understanding pricing models is crucial to make informed decisions.
Case Studies in Injection Molding Success
A few exemplary case studies showcase the impact of skilled injection mold makers:
- Case Study 1: A leading automotive manufacturer partnered with an injection mold maker to develop a complex dashboard component, resulting in a 30% reduction in lead time.
- Case Study 2: A healthcare company worked with a mold maker to produce a series of medical devices that required strict compliance with FDA regulations. The result was a seamless production run with zero defects.
- Case Study 3: A consumer goods firm utilized innovative mold designs that reduced material usage by 20%, achieving both cost savings and environmental benefits.
Future Perspectives for Injection Mold Makers
As manufacturing continues to evolve, the future for injection mold makers looks promising. They are positioned to spearhead advancements in:
- Customization: Increased consumer demand for tailored products will drive innovation in mold-making techniques.
- Collaboration: Partnerships between mold makers and product designers will foster creativity and efficiency.
- Globalization: Access to international markets will expand the footprint of injection mold makers.
- Regulatory Compliance: Continued emphasis on compliance will see mold makers adopt stricter quality measures.
Conclusion
The role of injection mold makers is indispensable in various industries due to their expertise and intricate understanding of the injection molding process. They are the backbone of modern manufacturing, enabling the production of high-quality parts with efficiency and precision. As technology advances, the potential for innovation and growth in this sector continues to expand, making it a vital area of focus for businesses aiming to lead in their respective markets.