Transforming Business Operations with Rapid Prototyping Plastic
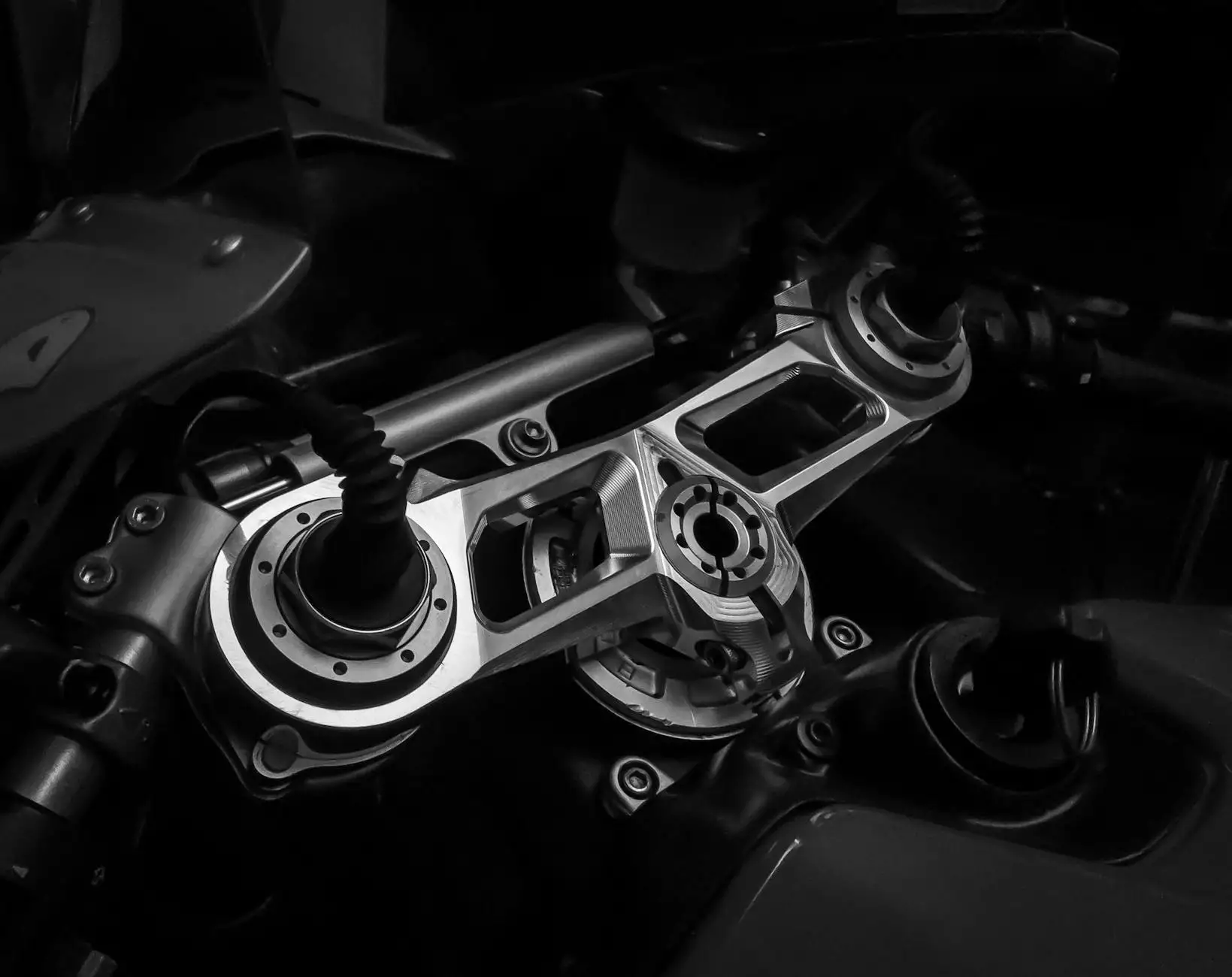
In the fast-paced world of modern manufacturing, efficiency and speed are paramount. Businesses are constantly seeking innovative ways to reduce production times and costs while improving product quality. One of the most significant advancements that have come to light in recent years is rapid prototyping plastic. This technology has paved the way for businesses to streamline their operations, enhance collaboration, and deliver superior products to market faster than ever before.
What is Rapid Prototyping Plastic?
Rapid prototyping plastic refers to a range of manufacturing processes that allow for the quick fabrication of physical parts using plastic materials. This technology enables businesses to turn their ideas into tangible prototypes in a matter of days or even hours, significantly shortening the traditional product development cycle. The essence of rapid prototyping is to create multiple iterations of a product quickly, facilitating testing and refinement before full-scale production begins.
The Importance of Rapid Prototyping in Business
In today's competitive landscape, the ability to innovate rapidly is crucial. Here are some core reasons why businesses should consider adopting rapid prototyping in their operations:
- Faster Time-to-Market: Rapid prototyping allows for swift design iterations, enabling companies to bring their products to market more quickly.
- Improved Product Quality: By identifying design flaws early in the process, businesses can enhance overall product quality.
- Cost-Effectiveness: Reduces the costs associated with traditional prototyping methods, minimizing waste and excess spending.
- Enhanced Collaboration: Designers, engineers, and stakeholders can work together more effectively with tangible prototypes to visualize concepts.
- Customization Flexibility: Rapid prototyping allows for easy adjustments in design based on user feedback and testing results.
Applications of Rapid Prototyping Plastic
The versatility of rapid prototyping plastic makes it applicable across various industries. Here are some prevalent uses:
1. Automotive Sector
The automotive industry utilizes rapid prototyping for designing components, testing fit and function, and validating designs before moving into mass production. Prototyping parts such as dashboards, housing for electronics, and various enclosures helps manufacturers reduce time and enhance performance.
2. Aerospace Industry
In aerospace, the need for precision and reliability is paramount. Rapid prototyping allows engineers to create intricate parts that meet strict safety and performance criteria. It aids in testing aerodynamic components and facilitating complex designs that would be challenging with traditional manufacturing methods.
3. Consumer Electronics
Consumer electronics companies rely heavily on rapid prototyping to develop new products. By producing prototypes of devices like smartphones or tablets, manufacturers can quickly revise designs based on user experience testing, ensuring that the end product meets customer expectations.
4. Medical Devices
In the medical field, rapid prototyping is instrumental in developing devices tailored to specific patient needs. This technology enables the creation of custom implants, surgical tools, and assistive devices that enhance patient care and outcome.
5. Architectural Models
Architects and builders utilize rapid prototyping to create detailed models of buildings and structures. These prototypes serve as essential tools for visualizing spatial designs and making adjustments based on project requirements and client feedback.
Materials Used in Rapid Prototyping
Choosing the right material is crucial for effective rapid prototyping. Plastics are among the most popular materials due to their versatility and ease of processing. Common materials include:
- ABS (Acrylonitrile Butadiene Styrene): Known for its strength and impact resistance.
- PLA (Polylactic Acid): A biodegradable plastic ideal for prototypes requiring intricate details.
- nylon: Offers durability and flexibility, making it suitable for functional prototypes.
- Polycarbonate: Known for its high strength and transparency, used in applications requiring visibility and toughness.
- TPU (Thermoplastic Polyurethane): Ideal for creating flexible and elastic parts.
DeepMould.net: Your Partner in Metal Fabrication and Rapid Prototyping
At DeepMould.net, we understand the significance of rapid prototyping in enhancing business agility and decision-making processes. We pride ourselves on being a leading provider of metal fabrication services, offering cutting-edge solutions tailored to meet our clients' needs. Our team of experienced professionals is committed to delivering high-quality prototypes that not only meet industry standards but also exceed customer expectations.
Why Choose DeepMould.net?
- Expertise in Diverse Industries: Our expertise spans automotive, aerospace, medical, and consumer electronics, ensuring we can tackle any project with proficiency.
- State-of-the-Art Technology: We invest in the latest prototyping technologies to provide our clients with the best quality prototypes rapidly.
- Customer-Centric Approach: We prioritize our clients’ needs and work collaboratively to deliver solutions that align with their vision.
- Flexible Production Capabilities: Whether you need small runs or large-scale production, we can accommodate your requirements.
- Commitment to Quality: Quality assurance is key at DeepMould.net, ensuring each prototype meets the highest standards before delivery.
Process of Rapid Prototyping at DeepMould.net
Our rapid prototyping process is designed to be straightforward, efficient, and effective. Here’s how we operate:
1. Initial Consultation
We begin with an in-depth consultation to understand your project requirements, objectives, and any specific design challenges. This collaborative dialogue sets the foundation for a successful outcome.
2. Design Development
Our experts use the latest CAD software to create comprehensive design models based on your specifications. We encourage client collaboration during this phase to ensure alignment with your vision.
3. Prototype Fabrication
Once the design is finalized, we proceed to fabricate the prototype using rapid prototyping plastic. Our advanced machinery and skilled technicians guarantee precision and attention to detail.
4. Testing and Iteration
The prototype is thoroughly tested to assess functionality and quality. Any necessary adjustments are made based on feedback and testing outcomes, ensuring the final product meets your expectations.
5. Final Review and Delivery
After refining and confirming the prototype’s quality, we conduct a final review before delivering the prototypes to your facility. We ensure timely delivery to support your project timelines.
Conclusion
In conclusion, incorporating rapid prototyping plastic into your business operations is not just a trend – it's a necessity for companies looking to thrive in today's competitive environment. With the ability to reduce time-to-market, improve quality, and foster innovation, rapid prototyping empowers businesses across various sectors to unlock their potential.
DeepMould.net stands at the forefront of metal fabrication and rapid prototyping, offering tailored solutions that drive success. Whether you're in the automotive, aerospace, medical, or consumer electronics industry, our commitment to excellence and customer satisfaction ensures that your prototyping needs are met with professionalism and precision.
Ready to elevate your business with rapid prototyping? Contact DeepMould.net today and discover how we can assist you in transforming your ideas into reality.